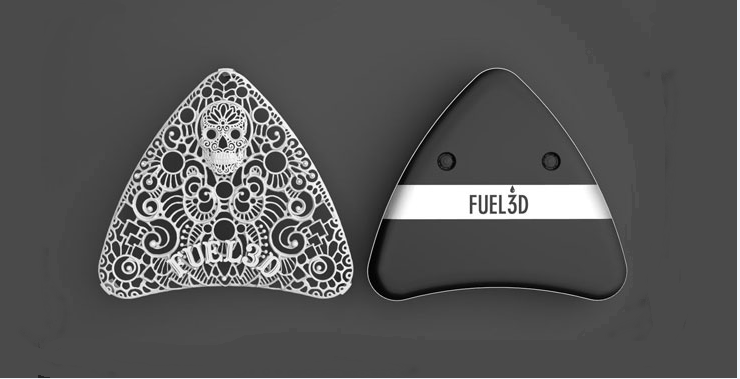
A 3D scanner is a device that allows the user to scan a three-dimensional object and save the information onto a computer. The scan can then be used for 3D printing, saving time and effort instead of creating a 3D model from scratch. 3D scanners scan surfaces that are in view, creating point clouds of geometric samples, and typically require several scans from different angles of a single object. All of the scans need to be brought into a common reference system, aligned, and merged to create a complete 3D model. From point clouds to applications; there is a choice of Polygon mesh models, surface models and solid CAD models.
The solid CAD model is easily editable and is the most common in the industry and saves files in STL format. Polygon mesh models are typically uneditable and are useful mainly as visuals. Surface models are somewhat more editable, but primarily for pushing and pulling the surface. The STL file is sent to the printer where it is printed.
The use of scanners can be especially effective in creating 3D models of objects that are too fragile for traditional plaster methods, such as archaelogical finds, which can then be 3D printed. 3D scanners can also be used in dentistry as a replacement for tedious plaster casts, to create scans of crime scene evidence, or to use ordinary objects for the use of video games and animation. In 3D printing, the use of a scanner is useful to create additional models of a favorite statue or toy and can aid in the printing of a model or part that needs to be replicated.
There are different technologies available for 3D scanners: contact and non-contact. Non-contact scanners can be divided into two categories: active scanners and passive scanners. Contact 3D scanners probe the object through physical touch. The object is held in place by a fixture or rests on a precision flat surface plate. Non-contact active scanners, similar to a camera, use some kind of radiation or light to detect the object's reflection or radiation and are typically less expensive. Non-contact passive scanners rely on detecting reflected ambient radiation, typically visible light.
Types of 3D Scanners:
Time-of-flight 3D laser scanner is an active scanner that uses laser light to probe the object, which uses a time-of-flight laser range-finder.
Triangulation 3D lasers are also active scanners that use laser light to probe the environment. The triangulation laser shines a laser on the subject and uses a camera to look for the location of the laser dot. Depending on how far away the laser strikes a surface, the laser dot appears at different places in the camera's field of view.
Hand-held laser scanners create a 3D image through the triangulation mechanism described above.
Structured light 3D scanners project a pattern of light on the object and look at the deformation of the pattern on the object.
Modulated light scanners shine a continually changing light at the subject. A camera detects the reflected light and the amount the pattern is shifted by determines the distance the light travel, with no interference from light sources other than a laser.
Non-contact passive scanners rely on detecting reflected ambient radiation. Most 3D scanners of this type detect visible light.
To learn more about the latest in 3D Printing, check out our 3D printing.